Flying probe testers are the only solution to test the complex PCBA of today. They combine the test accuracy of the latest ATE technologies along with the motion technologies to probe the smallest of small components like 01005 or even the 03015 metric components accurately and test them reliably.
They are increasing used today not only at the proto level to test the boards or for the repair of boards in the repair labs, they are being used in the production testing due to advancement in the motion technologies and latest test methodologies of accessing the boards on both side simultaneously, thereby reducing the test time.
PILOT NEXT> LINE is the new generation of Seica solutions for flying probers with a sleek, modern look and the most innovative technology around. This is the new generation of flying probers featuring a renovated and sleek look thanks to the premium materials of the chassis, and innovative electrical worth discovering performances, undoubtedly the most complete flying probing test platform on the market.
Moreover, all the PILOT NEXT> testers feature the Industrial Monitoring solution “4.0 ready” by Seica, to monitor current absorption, supply voltage, temperature, light indicators and other parameters useful to indicate the correct operation, to ensure predictive maintenance and make the systems compatible with the new standards of the fourth industrial revolution ongoing nowadays.
ADVANTAGES OF FLYING PROBE TEST
- Elimination fixturing costs and time
- Fast test program development, easy integration of design changes
- Process flexibility
- Circuit access, even in the absence of test points
- Controlled probe contact, programmable for any type of board
- Different test solutions and approaches integrated in a single test system
- Intrinsic positioning and measurement precision
INDUSTRY 4.0
Information and the technology needed to collect and analyze data, is key to the successful digitalization of the manufacturing process, which is at the heart of the Industry 4.0 concept. The PILOT NEXT> LINE has all of the capabilities needed for implementation in any Factory 4.0 scenario, providing the possibility to plug in any proprietary or third party information system to achieve the desired goals.
DIFFERENT ARCHITECTURES FOR DIVERSE SOLUTIONS
- PILOT H4 NEXT> is a horizontal solution, available in manual or automatic version. Completely compliant with the SMEMA protocol, ensuring complete automation of the in-line test process. It has an architecture which permits the integration of additional pins and jigs to augment test coverage or to integrate other processes, such as on-board programming (OBP) of digital devices.
- PILOT V8 and PILOT V4 NEXT> optimize the test of “double-side” electronic boards, which require stimulus and measurement on both sides of the UUT simultaneously. The use of 8 (V8) or 4 (V4) probes distributed on both sides of the Unit Under Test enables full test coverage as well as faster test time, and the vertical architecture minimize vibrations during testing, ensuring maximum test precision and measurement stability.
- PILOT BT EV Battery Test system has been designed to measure the electrical connections of battery packs. It performs parallel and high-resolution Kelvin tests of 16 cells at once in its maximum configuration of 4 flying fixtures on the four heads. It can achieve high production rates of nearly 2400 battery cells per minute.
PILOT NEXT>: TEST ENVIRONMENTS
MANUFACTURING, REPAIR, REVERSE ENGINEERING, PROTOTYPING, NEW PRODUCT INTRODUCTION (NPI), and EV BATTIERIES TEST are the environments where the PILOT NEXT> solutions are implemented.
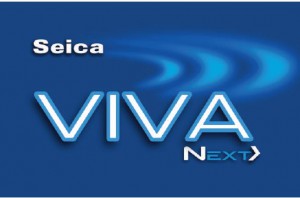
VIVA NEXT> is available in a 32 and 64 bit version with a new graphical interface and a guided environment for an easy and quick test program creation. It is fully integrated with NI-VISA drivers and with third-party test management software.
MANUFACTURING: the evolution of the test algorithms and strategies present in the VIVA NEXT> software mean that the PILOT NEXT> testers provide fast, high performance production testing.
The diverse, integrated test technologies allow the user to streamline the various production phases, optimizing process time.
EV Batteries test: flying probe test is the first standard automated solution adopted by battery manufacturers, and these systems are being widely used to measure the bonding resistances of the packs cells. Seica has chosen, with PILOT BT, the more innovative approach of developing a new solution, which addresses current and future battery test requirements in terms of speed, configurability and reliability.
REPAIR: there are different types of requirements for diagnosing faulty boards, depending on the characteristics of the boards themselves.
The PILOT NEXT> LINE has an extensive tool set developed to address all of the repair scenarios, and the intrinsic flexibility of the flying probe test approach allows the user to implement from one to all of the test techniques available.
PROTOTYPING AND NPI:
by exploiting the versatility of the PILOT NEXT> hardware and software, it is possible to obtain immediate data from the testing of prototypes, avoiding costs and time for building preliminary fixtures or test benches, ensuring maximum fault coverage in the minimum time.
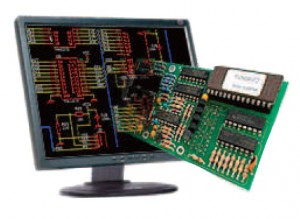
REVERSE ENGINEERING (RE): the necessity of managing field returns is a constant in today’s industy, the repair returns are often older boards which do not have complete documentation, schematics or construction data.
The double-side solutions offered in the PILOT NEXT> LINE are ideally suited to carry out reverse-engineering operations, and include all of the necessary software tools to enable the reconstruction of the electrical schematics and the CAD data of the board under repair. This helps to facilitate fault detection and repair, and to produce the documentation necessary for legacy support of the product.
PILOT NEXT>: THE NEW GENERATION
All of the solutions in the PILOT NEXT> LINE are equipped with excellent new performances for faster testing and higher fault coverage on even the most technologically advanced and complex boards of the latest generation electronic products and devices.
PILOT V8 NEXT> THE COMPLETE SOLUTIONS
- Maximum measurement precision
- Maximum positioning precision
- Test of 01005 and 03015 metric components
- Suitable for testing all types of boards
- Extremely fast test times
- Parallel test: two systems in one
- High level of traceability (integrated barcode reading)
- Industry 4.0 ready: easy remote monitoring and connection to information systems
THE AUTOMATED SOLUTION
In the vision of the Industry 4.0 factory of the future, the implementation of a highly automated, technologically advanced and reliable production line is essential.
The PILOT V8 NEXT> is part of the vision: in the
PILOT V8 NEXT>
- High flexibility
- Suitable for double- side board testing
- Suitable for prototype testing
- Suitable for reverse engineering
- Automatic loading/unloading
- Single Rack / MultiRack handling
- Automatic selection of test program
- Manual/Automatic solution
PERFORMANCE:
ICT, FlyScan, OBP, Thermal Scan, LED test, AOI functions, Reverse engineering
pass-through version, with dedicated loaders and unloaders, it is the operator-free test solution for the manufacturing environment.
PILOT H4 NEXT>
Automatic solution
- Easy connection to loader/unloader modules
- Allows the integration of dedicated frames and/or dedicated jigs
- Best for boards with single-side test access
Manual solution
- Allows the integration of dedicated frames and/or dedicated jigs
- Best for boards with single-side test access
PILOT NEXT> OPTIONS
aaaa
LED TEST
The LED sensor option is used for testing the LEDs present on the UUT. The UUT is powered on, and the LED sensor measures luminosity, color, saturation and frequency spectrums of the LEDs, operating in the visible and infrared light range of wavelengths.
aaaa
HD CAMERAS
The PILOT NEXT> systems are equipped with high definition color cameras which, together with new, sophisticated software algorithms, enable an advanced level of optical inspection of the UUT, complementing the electrical tests with the verification of presence/absence, polarity.
In addition they are used for automatic centering of fiducials, reading barcodes and for the acquisition of the board image for offline programming development and support during fault diagnostics and repair.
aaaaaaa
MARKER
The optional UUT test marker can be installed on any PILOT NEXT> system, for visual test traceability and subsequent identification purposes.
aaaaa
SPECIAL TEST SEQUENCES AND OBP
VIVA NEXT> software can call, during test program execution, functional test sequences written using third party languages: for example LabviewTM, VBScript, Python, and C, allowing the user maximum test flexibility. The PILOT NEXT> systems also offer fully integrated On Board Programming solutions, applied to the UUT via the mobile system probes.
aaaaaaaaa
TRACEABILITY
The PILOT NEXT> systems include a of hardware and software features and performances to support full traceability of the test results of each single UUT: the cameras automatically read 2D barcodes allowing test results to be stored for each board, making them available for subsequent repair operations, statistical analysis, etc., whether locally, via the resident repair station module, or to external information systems.
aaaaaaa
THERMAL SCAN
The thermal Scan module verifies the operating temperatures of the circuits and components on the UUT, comparing them to the temperature profile acquired on a powered on sample board. Like all other test techniques available in VIVA NEXT>, thermal scan tests are fully integrated into the complete test program for the specific board.
aaaaaaaa
AOI AND RGB LIGHTING
The PILOT NEXT> systems integrate new, improved RGB lighting: the advanced filters and color programming options allow the user to achieve the best conditions for automatic optical verification of component and solder presence.
aaaaaaa
VECTORLESS TECHNIQUES
There are two vectorless test techniques available on the PILOT NEXT> systems used to check for process faults on ICs (typically shorts and unsoldered pins), fully integrated in the test program:
Autic: based on clamp diode measurements.
Openfix: performed via a capacitive sensor which measures the response of all of the pins of the IC under test.
aaaaaaaaa
AUTOMATED LASER INSPECTION
The Automated Laser Inspection option provides an accurate measure of the height of objects, providing an additional test for presence/absence of component bodies, PCB thickness and warpage measurement. Fast and reliable, it can be also applied to any mechanical assembled part on the PCB. Available for both Top and Bottom sides.
aaaaaa
NET-ORIENTED TEST:
FNODE-PWMON
The net-oriented test techniques included in the PILOT NEXT> systems significantly reduce the number of measurements required for in-circuit test, therefore test time, without sacrificing fault coverage.
FNode: stimulates and compares the analog behavior of the nets on the UUT to those on a golden sample board.
PWmon: stimulates and compares the behavior of the board nets in the power on condition with respect to a golden sample board. This test technique is applicable to both analog and digital nets.
aaaaaaaaaaa
QUICK TEST
This simple and intuitive software interface enables the user to create customized functional tests by simply clicking on the various system resources displayed to connect them to the UUT.
aaaaaaaaaa
PARALLEL TEST
The architecture of the PILOT NEXT> offers the possibility to execute parallel testing of two single or double-side boards. This capability has a significant impact on test throughput, doubling it in the first case, and in the second case, achieving a significant increase, as well as the ROI of the test system.
aaaaaaaaaaa
FLYSCAN
This option brings a fully integrated solution for flying probe boundary scan testing. The boundary scan tests are generated automatically along with the other electrical tests by the VIVA NEXT> software, and are executed as part of the complete test program. A single test report includes the boundary scan results, and in the case of faults, further tests are carried out via the flying probes to provide component-level diagnostic information, usable in the VIVA NEXT> Repair Station environment. The “extended test“ feature also enables the jtag-type test of non jtag nets, eliminating the need to create manual cluster tests reducing programming time and increasing fault coverage.
aaaaaaaaaaaa
PRBOOST
The Prboost option will bring to each of the eight electrical probes up to 2A to give the maximum flexibility to power up the UUT.